日本特殊陶業株式会社を設立
日本ガイシで点火プラグを9年間研究
絶縁部品の「がいし」メーカーであった日本碍子において、技術者であった江副孫右衛門氏が海外で普及しつつあった点火プラグに着眼。そこで、大正10年(1921年)から自動車向けの点火プラグの研究開発を開始した。
しかし、通常の陶器とは違い「電気絶縁性能・強度・急熱急冷(60度〜2000度)への耐性」が必要であり、絶縁体の原材料の模索や、焼成技術の確立に時間を要した。
その後、直下式磁気焼成用トンネルの生産設備を完成させ、点火プラグの実用に耐える磁器(絶縁体)を開発し、販売に目処を立てた。
プラグの販売開始
1926年に試作品として1000個のプラグを生産したが、不良品が2〜3個発見されたため、販売計画を中止。点火プラグの品質は、自動車の性能に影響することから品質管理を徹底するまでは発売を見送った。
その後、歩留まりの改良を経て、1930年から自動車向けの点火プラグの製造販売を開始した。このため、研究開始から実用化までに約9年を費やす形となった。
1930年代を通じてトヨタ自動車などの国内自動車メーカーが成長したことを受けて、点火プラグの需要も増大した。
日本ガイシから日本特殊陶業の分離
自動車の国産化により増大する点火プラグ需要に対応するため、日本ガイシは点火プラグ事業の分離を決定。1937年に別会社として日本特殊陶業を資本金100万円で設立。日本ガイシの隣接地にて、日本特殊陶業の本社工場を竣工し、自動車向けて点火プラグメーカーの製造・販売を開始した。
日本特殊陶業の初代社長には、日本ガイシで点火プラグの開発の従事し続けた江副孫右衛門氏が就任。会社設立時点で従業員数259名の規模で操業を開始した。
戦時中を通じて点火プラグの輸入(独ボッシュ社、米AC社など)が途絶したことにより、日本特殊陶業に対する点火プラグの注文が増大。国産自動車メーカーに対して、国産点火プラグを納入することで業容を拡大した。
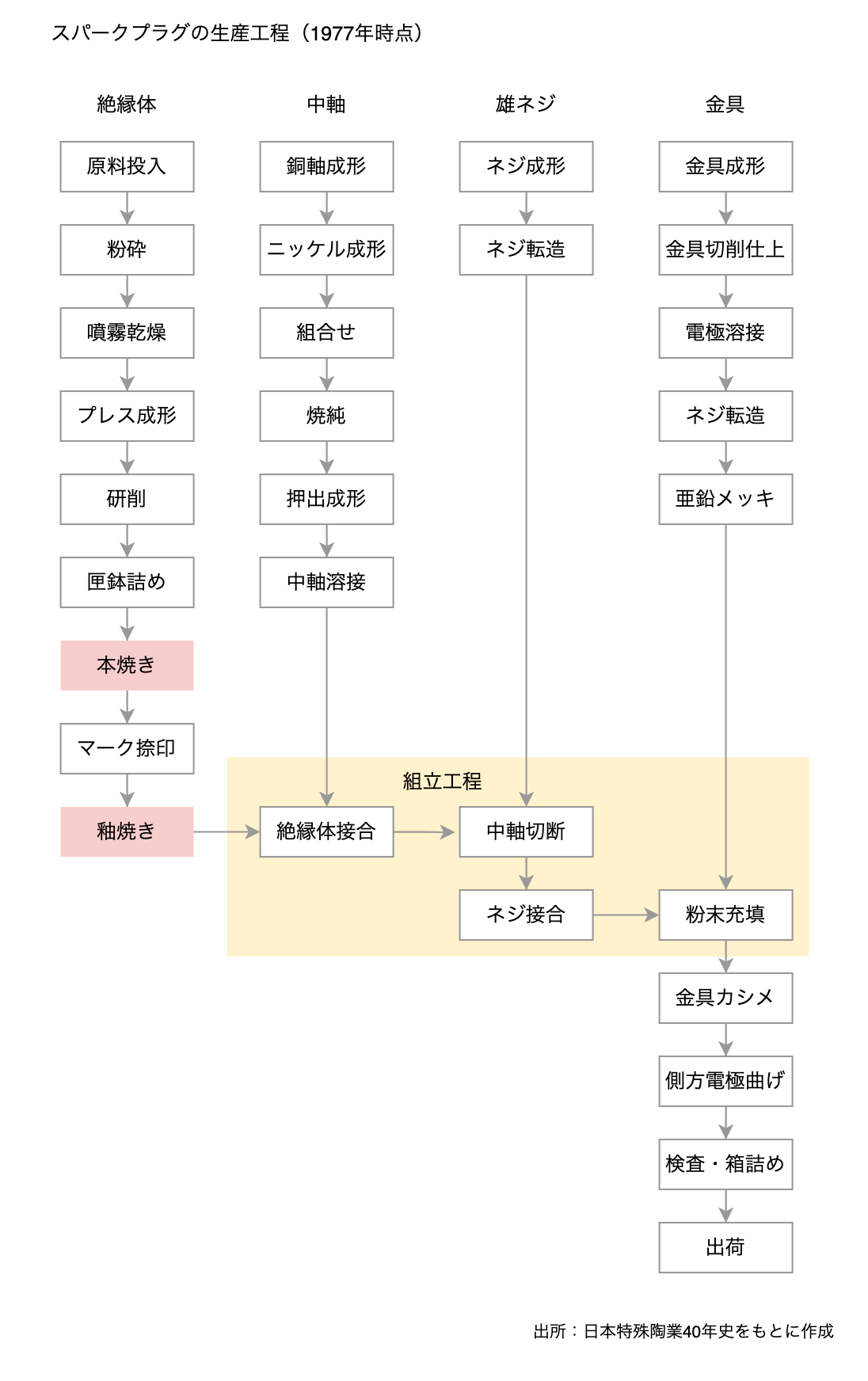
終戦により2000名を解雇
戦時中を通じて航空機向け点火プラグを製造して軍需に対応。1945年3月時点で従業員数2,887名の規模に発展した。
しかし1945年に終戦を迎えると、日本特殊陶業は人員整理を決定。従業員数約200名が残り、約2600名の人員を解雇した。
東京証券取引所に株式上場
スパークプラグの生産改善
1956年に日本特殊陶業の経営陣が米国の大手プラグメーカーを視察。これらの海外メーカーの工場における生産性が優れており、その理由を工程全体に新鋭機械を導入している点にあると判断した。これは、スパークプラグはグローバル規格品(少品種)かつ量産品(1959年当時・単価190円)であり、生産工程の合理化メリットの効果が大きいためであった。
そこで、日本特殊窯業では、部分的な機械化ではなく生産工程全体における機械化を遂行。この結果、既存工場における生産能率を2倍に改善した。
昭和31年でしたか、アメリカの3大プラグ会社を見ることができました。3大プラグ会社というのは、チャンピオン、AC、オートライトです。この3工場を見ていまして、非常に感じるところがありました。機械それ自体は、うちと大同小異ですが、労働生産性には数倍の開きがある。どこでこうも開きができるのか、つくづく考えてみますと、われわれの設備は片輪なんです。
われわれは、優秀な機械を揃えるにしても、全体を優秀な機械にするということではなく、部分的に能率のいい機械を買う。だから工場の中の生産工程がアンバランスになる。能率のいい機会では、品物が出来すぎてたまるか、機械自体にアンバランスがあるため、どうしても人間のロスが出る。
機械のバランスをとり、機械と機械のつなぎをオートマチックに持っていくと、品質管理もやりやすいし、機械につく人間も少なくて済む。ランニング・ストックも少なくなる。こうしたことが生産性に大きく関連してくるわけです。
わたくしは、アメリカから帰るとすぐ、向こう半年の間に能率を倍にしたいと、それぞれ適切な指示を与え、みんなにも提案させるようにしたんです。その効果は覿面で、半年ぐらいの間に基礎ができ、能率がグンと上がりました。倍近くになったはずです。
ブラジルで点火プラグの現地生産を開始
ブラジル政府からの工場誘致の依頼を受け、日本特殊陶業はブラジルでの現地生産を決定。100%子会社として現地法人を設立し、1959年にブラジルでの生産を開始した。販売先は、ブラジルで現地生産される欧米系の自動車メーカーで「GM、ウイリス、シムカ、フォルクスワーゲン」などであった。これはスパークプラグには国際規格が存在しており、車種やメーカーごとにプラグの品種が異ならないためであった。
この結果、現地法人の業績は好調に推移。1966年の時点で、組付用で現地シェア80%・補修用で同40%を確保した。
ただし、ブラジル政府は「配当金禁止措置」を実施しており、日本特殊陶業はブラジル現地法人の利益を本社が確保することはできず、ブラジルの現地で再投資する形となった。
小牧工場を新設・プラグ増産体制へ
1960年に日本特殊陶業は小牧市内において、大規模な工場用地(9万平方メートル)を確保。1961年に日本特殊陶業は小牧工場を新設。続いて、1966年には小牧工場に第二工場を新設して、点火プラグの量産体制を確立した。その後も増設を続け、1975年までに第10工場を新設した。
1969年には追加の用地として、小牧工場の隣接地(2.9万平方メートル)を取得。このほかに社員療の土地も取得し、1970年代の時点で小牧工場の敷地面積は14.7万平方メートルに及んだ。
1960年代を通じて乗用車が国内に普及(モータリゼーション)したため、点火プラグの需要も増大。日本特殊陶業は、小牧工場の新設による増産により、需要増加に対応した。
点火プラグで国内シェア70%を確保・補修用で高収益
1966年時点の点火プラグの国内生産量ベースで、日本特殊陶業はシェア70%を確保した。競合はデンソー(ボッシュと技術提携)および日立製作所であったが、日本特殊陶業が国内生産を独占する構図であった。陶器の焼成に高度な生産技術が必要なため、参入企業が限られる事業であった。
業績面でも高収益を確保。完成車メーカー向けの点火プラグに加えて、補修用(スパークプラグは消耗品の側面がある)の点火プラグも全国に販売網を形成して対応。特に補修用は完成車用に比べて「メーカーから価格圧力」が少ないため、高収益を確保する原動力になったと推定される。
現在わが国の点火プラグ業界は、日本特殊陶業のほか、日本電装と日立製作所の3社で全国需要のほとんど全てをまかなっている。しかも、このなかにあって、日本特殊陶業の地位は絶対的である。その生産するNGK点火プラグは、全国生産の7割強を占めている。つまり全国津々浦々を走り回る自動車の100台のうち、70台以上がNGK点火プラグを使っているわけだ。とくに国産の新車には、その9割までが組み付け用純正部品として、これを採用している。
米国に現地法人を設立
補修用点火プラグの販売拡大のため、米国ロサンゼルスにて「米国NGK」を設立。現地ディーラーの開拓を開始
セラミックICパッケージの製造販売を開始
半導体(集積回路)向けのパッケージ素材として1960年代を通じてセラミックが台頭。これを受けて、日本特殊陶業は1962年に「半導体セラミック部門」を新設してパッケージの研究開発を開始し、1967年にセラミックICパッケージの製造販売を開始した。
パッケージに着眼した理由は、点火プラグの原材料が「アルミナ」であり、パッケージも同様に「アルミナ」による焼成が可能であったためである。ただし、セラミックICパッケージでは、同じくアルミナの加工に強みがある「京セラ」が先発しており、日本特殊陶業は後発参入となった。
半導体の需要増加とともにパッケージの売り上げを拡大し、日本特殊陶業は「自動車向け点火プラグ」に加えて、「半導体向けセラミックパッケージ」の新規展開により全社売上を拡大した。1993年時点の世界シェアは2位(30%)であり、世界シェア1位の京セラ(60%)に追随した。
スーパープラグの値上げ実施
1958年時点でスパークプラグ1個あたり190円の価格設定をしていたが、1970年4月から新製品「NGKスーパー」については250円に設定。1972年1月からは全品において250円に改定した。その後、オイルショックによる物価高騰により、1975年6月には360円に改定。
東南アジアでの現地生産を本格化
欧・米・豪で販売拠点を拡充
自動車向け酸素センターに参入
1982年に日本特殊陶業は、自動車の排ガス濃度を検出する装置「酸素センサー」の製造販売を開始。排ガス規制によるニーズ増加に対応した。
ただし、1975年にデンソーが酸素センサーに参入して先発していたため、日本特殊陶業は後発に相当した。このため、点火プラグで培った販路を活用し、米国など海外での販売(輸出)に注力した。1985年には米フォード、1986年にはクライスラー向けに酸素センサーの大量納入を実現したことで、酸素センサーは国内ではなく北米向けに展開した。
先進国での現地生産を本格化
インテル向けの樹脂PKGの量産を本格化
1990年代を通じてCPU/MPU向けのパッケージ素材について、樹脂製(プラスチック)の価格低下によりセラミックからの素材転換が具現化した。これは、1960年代から続いたセラミック製パッケージという前提が崩れることを意味した。
そして、1996年にインテルは半導体パッケージの素材を従来のセラミック(京セラ・日本特殊陶業が供給)から、プラスチック(イビデンが供給)に転換することを決定した。これにより、プラスチックパッケージに注力してきたイビデンが、日本特殊陶業と京セラの牙城を崩すことになった。
日本特殊陶業はプラスチックパッケージに対応するために、1998年にインテル向けの量産体制を確立。1998年6月時点で月産20万個、1999年初時点で月産160万個の生産体制となった。このため、日本特殊陶業は、プラスチックパッケージにおいても、イビデンに対して後発参入となった。
アジアでの生産増強
半導体向けパッケージの増産・小牧工場で増産計画
最終赤字に転落・セラミックICパッケージの再編
セラミックパッケージで巨額損失
リーマンショックによる半導体不況により、ICパッケージに対する需要が減少。日本特殊陶業は「ICパッケージ製造・遊休」の資産について、国内工場5箇所で減損損失として合計266億円を計上した。一部の製造拠点については、工場稼働の目処が立たず、減損計上を決定したと思われる。この結果、FY2008に日本特殊陶業は716億円の最終赤字に転落した。
機構改革により担当役員(副社長)を降格
2009年5月に日本特殊陶業は代表取締役の移動を発表。情報通信事業(セラミックICパッケージ)を担当してきた加藤氏(代表取締役副社長)が顧問に退くことを発表。一方で、専務取締役であった二名(川原氏・川下氏)が共に代表取締役副社長に就任した。なお、新任の副社長二名は自動車事業の出身であり、情報通信ではなく自動車関連事業が経営トップに就く人事となった。
すなわち、情報通信事業出身の加藤副社長の退任により、日本特殊陶業は「自動車関連事業」に注力する体制となった。
セラミックICパッケージの事業再編
2009年5月に日本特殊陶業はセラミックICパッケージにおける事業再編に着手。財務体質が悪化した製造子会社を1社に集約するとともに、セラミックICパッケージの製造を段階的に縮小した。以後、日本特殊陶業としては自動車関連事業に投資する方針を明確にした。
スパークプラグ10億本生産計画を公表
第6次中期経営計画を公表
2013年に日本特殊陶業は「第6次中期経営計画」を公表し、自動車関連事業(スパークプラグ)において2020年度末で「10億本」の生産目標を設定した。目標実現のため、設備投資計画においては自動車関連事業に集中投資を実施し、FY2013には約460億円を自動車関連に投じる計画を打ち出した。
設備投資の狙いは、部品ごとに生産工場を1箇所に集約することにあった。従来は異なる工場で同一の部品を製造していたが、新工場の建設を通じて、主要な部品ごと(絶縁体・主体金具・端子部品など)に、それぞれ1カ所の工場で集中生産することを狙いとした。
新工場の建設を伴うことから相応の投資が必要であり、日本特殊陶業としては、自動車向けに注力する姿勢を打ち出した。これは、日本特殊陶業のかつての主力事業であった「半導体向けのパッケージ」における投資を縮小し、事業の「選択と集中」を意味した。
二野工場を新設
スパークプラグ増産のために、絶縁体の生産拠点として二野工場(岐阜県可児市)を新設。第1期における投資額は280億円であった。なお、従来の主力拠点であった小牧工場は老朽化しつつあり、二野工場は小牧工場のリプレイスという側面もあった。
海外ではなく国内工場を選定した理由は、セラミック加工における生産技術の難易度が高く、国内の技術蓄積を生かすためであった。